Customization
Customized Planetary Reducer Process
Custom planetary reducers are designed to meet the unique demands of specialized industrial applications where standard gearboxes may not be sufficient. These demands may include specific working conditions, gear ratio requirements, space constraints, or additional functional needs. Our customization process follows the steps below:Applications


Requirement Analysis & Consultation
Custom planetary reducers are designed to meet the unique demands of specialized industrial applications where standard gearboxes may not be sufficient. These demands may include specific working conditions, gear ratio requirements, space constraints, or additional functional needs. Our customization process follows the steps below:Applications
- Torque, speed, precision, and noise levels
- Environmental conditions (temperature, humidity, corrosiveness)
- Mounting methods and spatial limitations
- Special functional needs (e.g., corrosion resistance, ultra-quiet operation)
Based on this discussion, our engineering team performs a preliminary feasibility assessment and identifies potential technical challenges.

Solution Design
Our design team formulates a preliminary solution based on the gathered requirements. This includes:
- Selecting the optimal gearbox structure and configuration
- Defining gear parameters, shaft dimensions, and planetary gear layout
- Choosing suitable materials for gears and components
- Designing the housing to fit installation constraints
We use advanced engineering software for mechanical analysis and virtual simulations to aa validate the structural integrity and performance of the design.
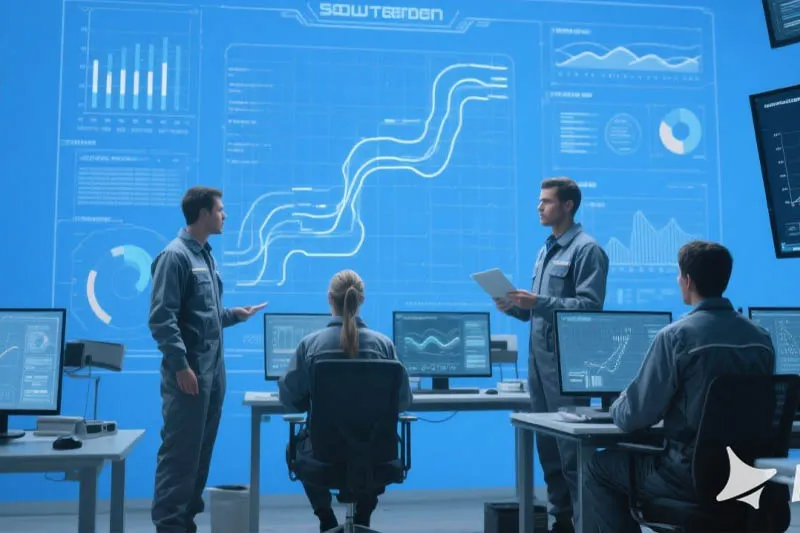
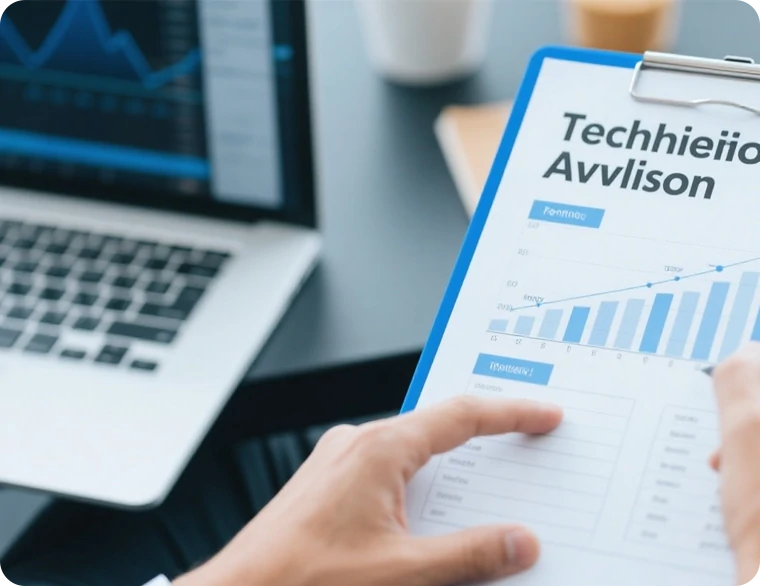

Technical Evaluation
A comprehensive technical review is conducted to assess:
- Structural strength and durability
- Gear life expectancy
- Mechanical efficiency
- Compatibility with application-specific constraints
Only designs that pass all technical benchmarks proceed to prototyping.

Prototype Manufacturing
Upon design approval, we manufacture a prototype using high-precision equipment and advanced manufacturing processes. This ensures that each component meets the design specifications. The prototype undergoes:
- Dimensional inspection
- Performance testing (torque, efficiency, accuracy)
- Durability and stress testing

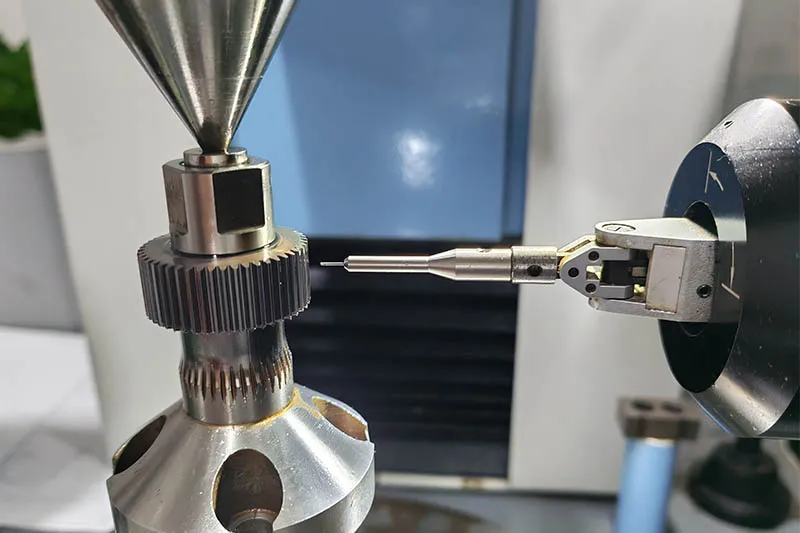

Performance Testing & Validation
Extensive testing is carried out to confirm the prototype meets both design and customer expectations. This includes:
- No-load and full-load operation tests
- Temperature rise evaluation
- Noise level measurements
- Long-term durability testing

Design Optimization (if needed)
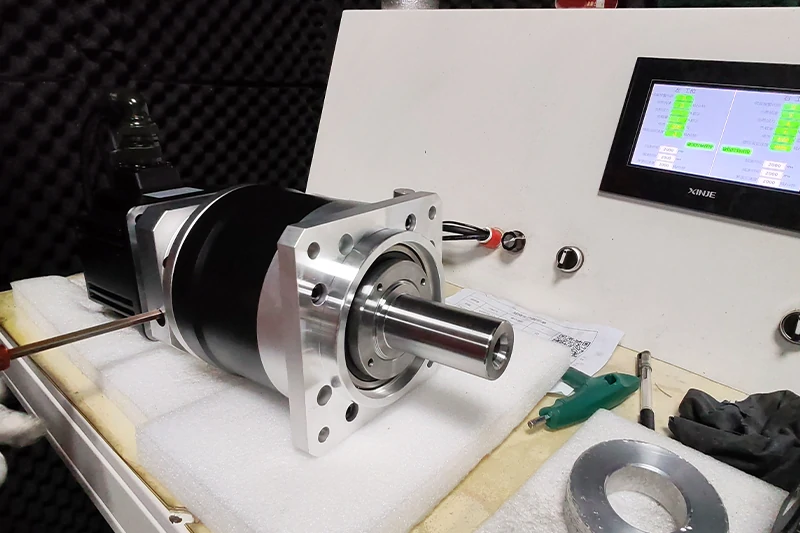
If test results indicate any issues or improvement opportunities, we refine the design. A revised prototype is produced and retested. This iterative process continues until all requirements are met. Close collaboration with the customer ensures alignment at every stage.

Customer Approval
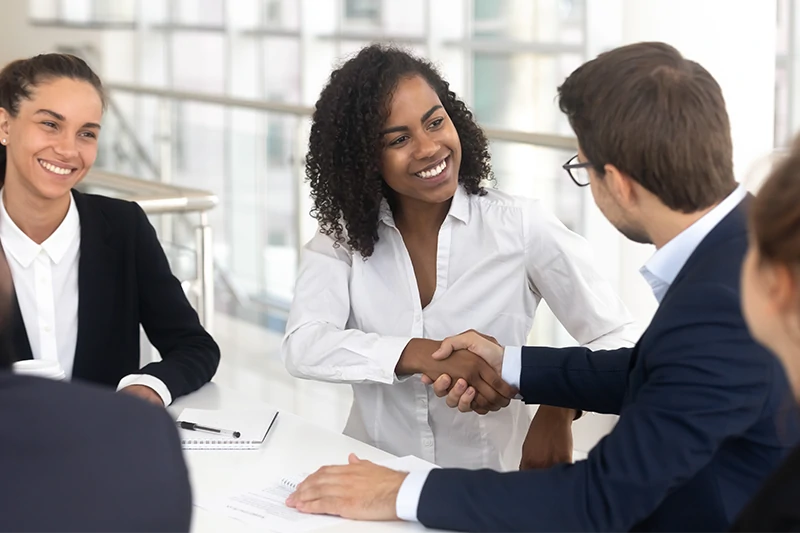
Once the prototype passes internal validation, it is delivered to the customer for field testing or evaluation in real-world conditions. If any adjustments are needed, we work closely with the customer to make necessary refinements.
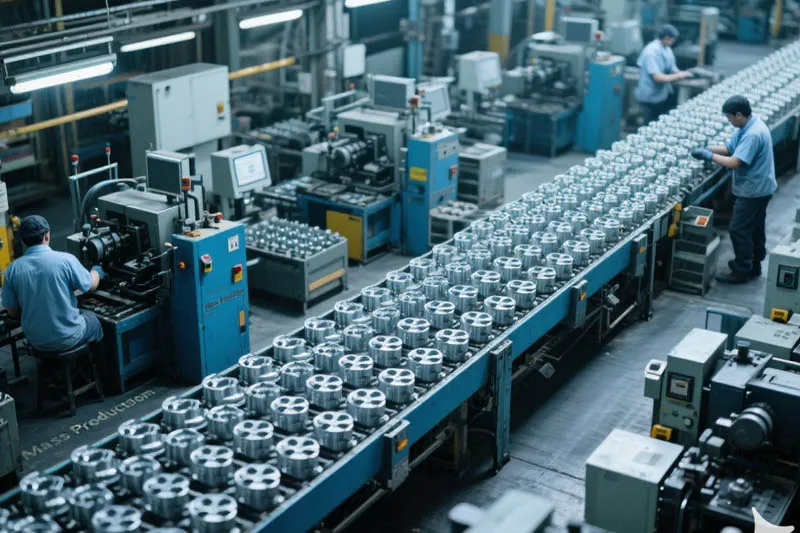

Mass Production
After customer approval and finalization of the design, the project moves to volume production. During this stage, we:
- Implement strict quality control throughout the manufacturing process
- Establish inspection protocols to ensure product consistency
- Perform random sampling and testing on finished products to guarantee reliability

Delivery & After-Sales Support
Finished products are delivered on schedule according to the agreed terms. We provide full after-sales support, including technical assistance, maintenance guidance, and warranty services to ensure long-term satisfaction and system performance.
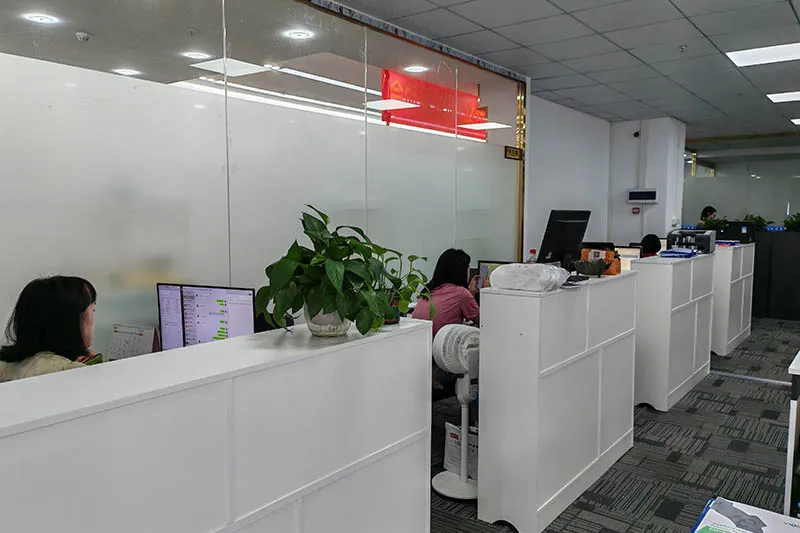