Gear Profile Inspection
Gear Profile Inspection: Verifying Gear Tooth Accuracy and Performance
What Is Gear Profile Inspection?
Gear profile inspection is the process of measuring the tooth geometry of gears, including involute shape, lead, pitch, and helix angle. Specialized gear inspection machines scan tooth flanks to detect form errors that can affect meshing performance and noise levels in planetary reducers.
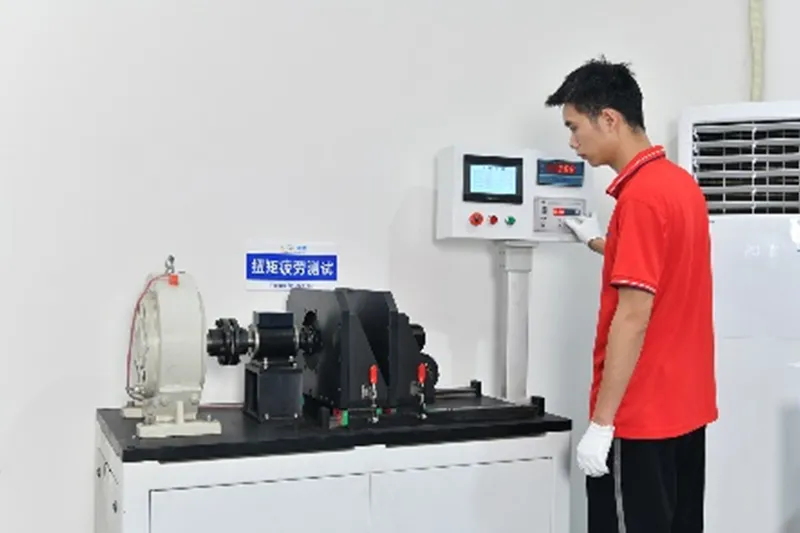
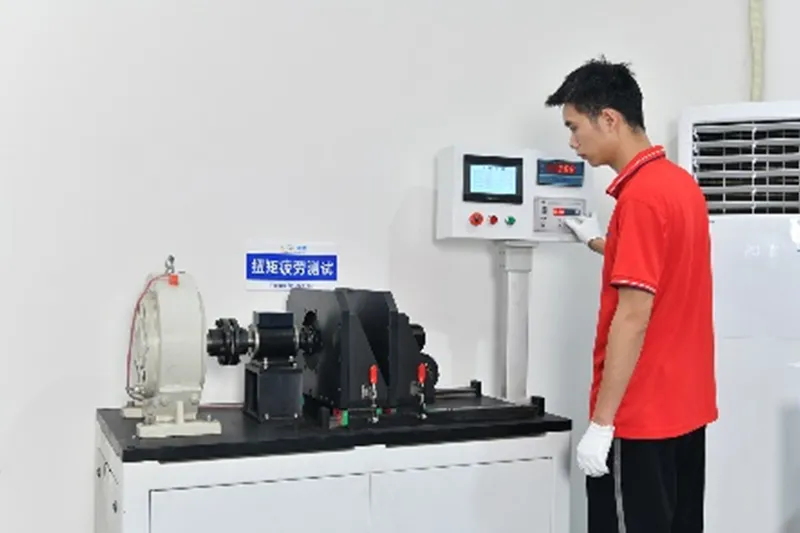
What Defines a High-Quality Gear Profile Inspection?
A precision gear profile inspection involves:
- High-resolution scanning probes or gear analyzers
- Measurement of tooth form deviation (Fα), pitch error (Fp), and lead error (Fβ)
- Comparison to standards (DIN 3962, AGMA 2000-A88)
- Accurate backlash and contact pattern simulation
These measurements ensure consistency across gear batches and high system performance.
Why Gear Profile Accuracy Matters in Reducers
Accurate gear geometry contributes to:
- Smooth, quiet meshing under load
- Even load distribution across teeth
- Reduced wear and pitting
- Consistent backlash and positioning control
Deviations in profile can lead to vibration, misalignment, and premature failure.
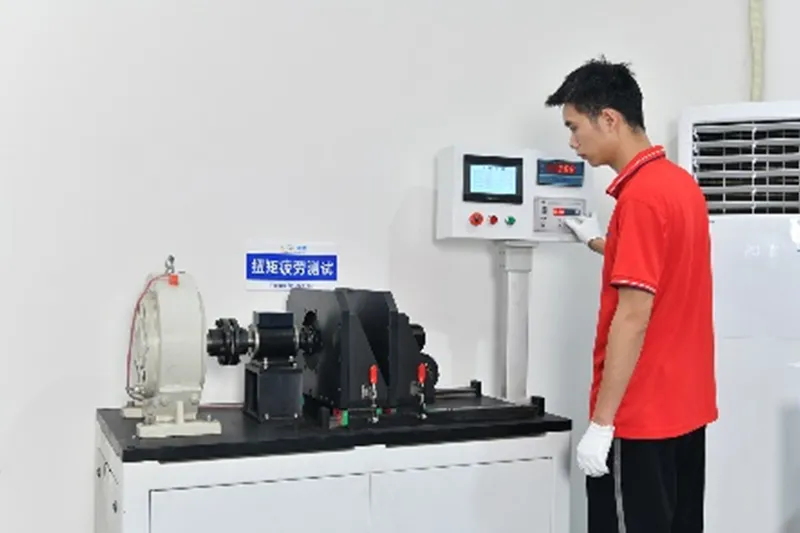
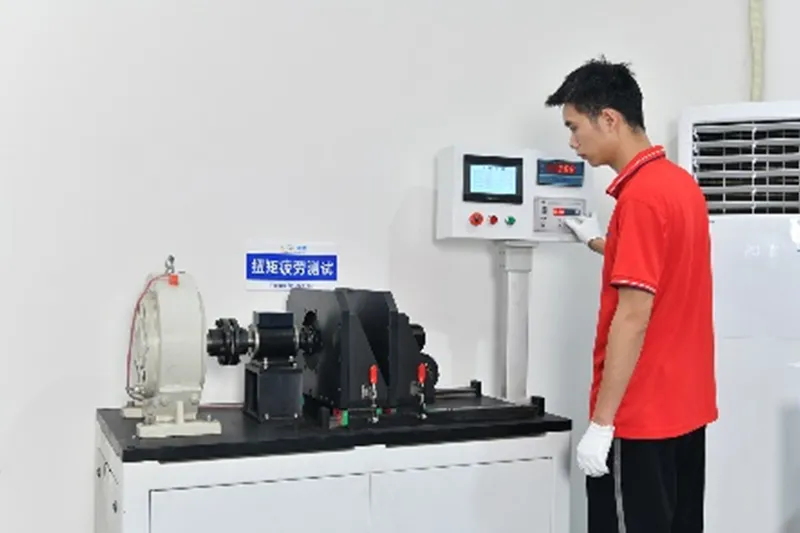
How VIGE Performs Gear Profile Inspection
We use state-of-the-art gear analyzers to inspect every gear batch. Our process includes:
- Full-tooth profile and helix scans
- Statistical process control for repeatability
- Inspection reports stored for traceability
- Regular calibration of inspection machines
This ensures all gear sets perform as expected in high-speed or precision applications.
Additional Benefits of Gear Profile Control
Strict profile inspection improves system efficiency and allows tighter reducer tolerances. Benefits include:
- Enhanced dynamic stability
- Lower transmission losses
- Longer service life
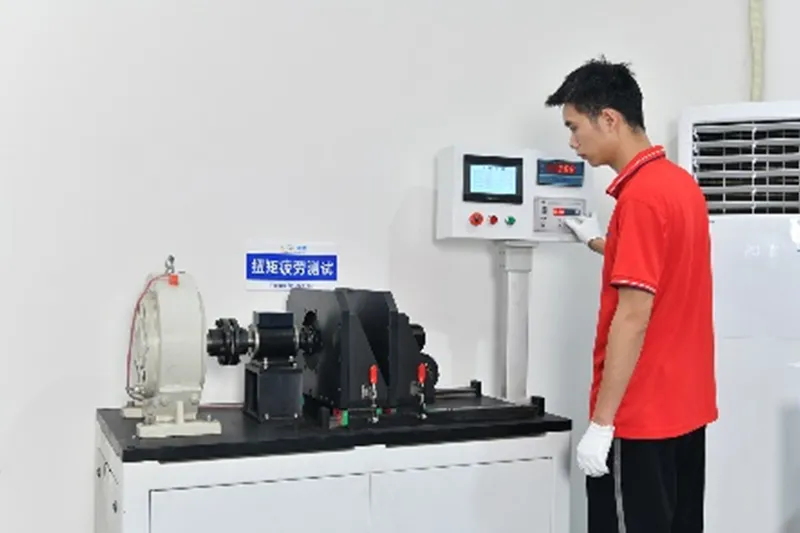