Hole Grinding
Precision Hole Grinding: Delivering High-Accuracy Gear Bore Finishing for VIGE Planetary Reducers
What Is Hole Grinding?
Hole grinding, also known as internal grinding, is a specialized precision machining process used to finish the internal bores of components — such as the center hole of a gear. This process removes minute amounts of material using abrasive grinding wheels, achieving highly accurate internal diameters, fine surface finishes, and tight cylindricity and concentricity tolerances. It is essential for high-precision gear and bearing fits in planetary reducer applications.
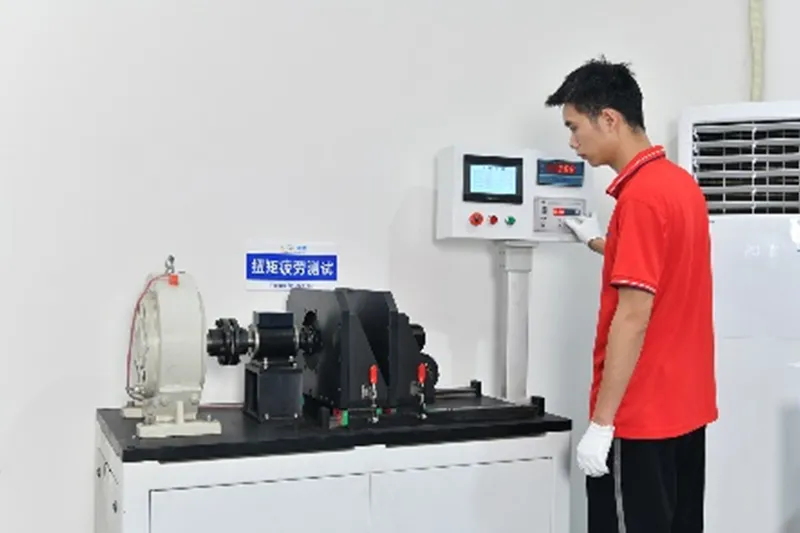
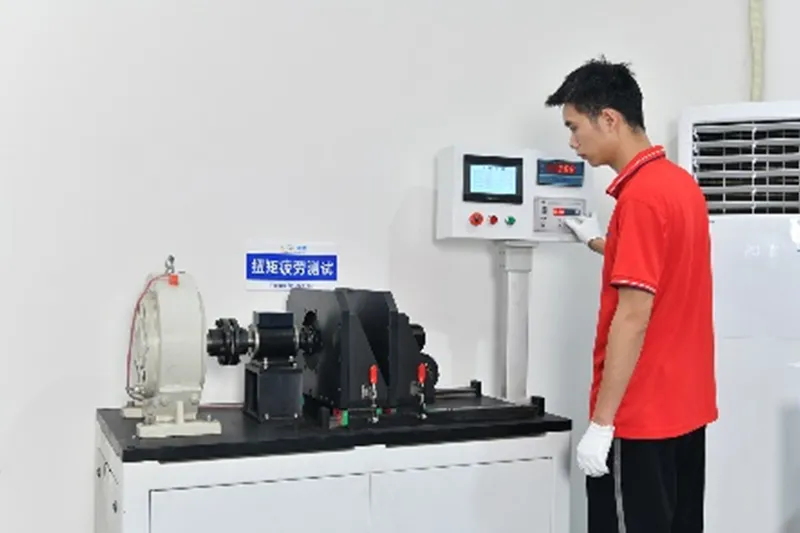
What Defines a High-Quality Hole Grinding Process?
What Defines a High-Quality Hole Grinding Process?
- Tight internal diameter tolerances (within microns)
- Perfect roundness and concentricity with the gear's outer profile
- Ultra-fine surface roughness for smooth fits (Ra ≤ 0.2 μm)
- No thermal damage or micro-cracking in the bore
At VIGE, we use a progressive grinding method — an advanced approach involving eight sequential grinding tools of varying grit size. This gradual refinement process progressively improves dimensional accuracy and surface quality at each stage, ensuring optimal geometry and finish.
Why Hole Grinding Matters in Planetary Gear Reducers
The internal bore of a gear directly interfaces with shafts, bearings, or couplings. Precision hole grinding ensures:
- Tight press-fit tolerances, improving torque transmission and alignment
- Improved bearing seating and lifespan
- Minimized vibration and noise, due to perfect balance and centerline alignment
- Corrosion resistance, as smoother bores resist moisture and rust buildup
- Reduced risk of assembly wear or deformation
In servo-driven or precision-loaded gearboxes, the consistency of bore finish has a significant impact on performance and durability.
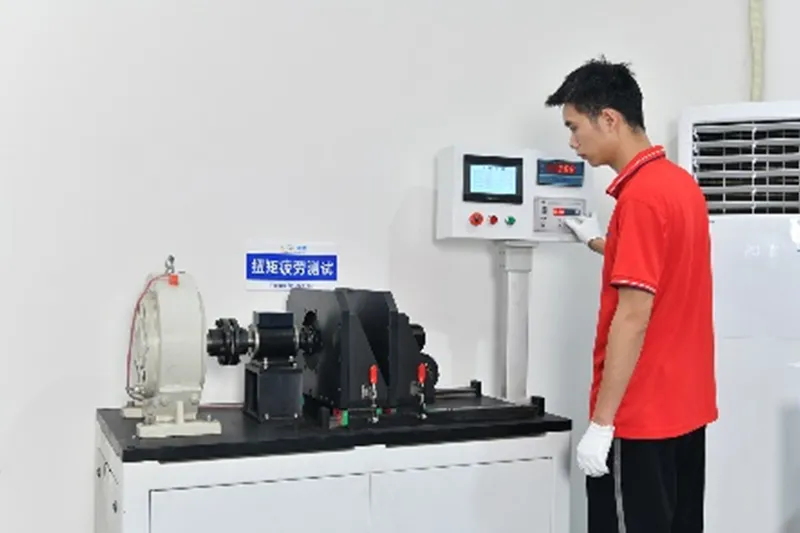
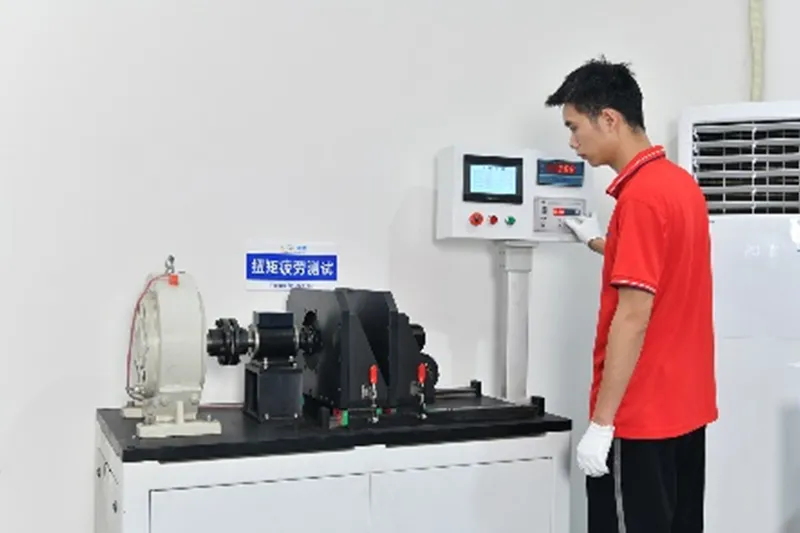
How VIGE Controls Hole Grinding Quality
Our hole grinding process is carried out on high-precision internal grinders equipped with:
- Automated progressive grinding stages (8-step refinement)
- Real-time internal diameter monitoring systems
- Surface finish testing tools for every batch
- Concentricity and roundness inspections using CMM and air gauges
Our climate-controlled production environment, combined with strict process control, ensures every gear bore meets the highest standards before entering final assembly.
Additional Benefits of Precision Bore Grinding
By achieving optimal bore geometry and surface integrity, precision grinding eliminates the need for post-assembly rework or adjustment. It ensures seamless shaft fits and enhances overall gearbox symmetry, contributing to:
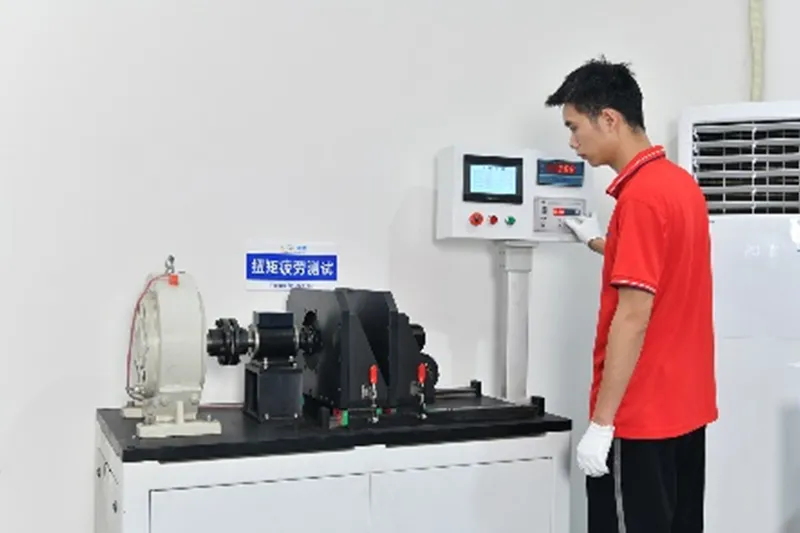