Right Angled Helical Gear Reducer - L Shape
Products
Right-Angled Helical Gear Reducer - L Shape
Right-Angled Helical Gear Reducer (L Shape) Combining helical gear precision with a 90-degree output structure, this right-angled reducer features a bevel-helical input stage for compact yet smooth torque delivery. The angled tooth profile provides low backlash and quiet performance, while gears are carburized and quenched to HRC58–62. A ductile iron housing and dual-bearing support ensure mechanical stability under load. With efficiency ≥98%, transmission ratios from 3 to 250, and return clearance ≤15 arc minutes, it is ideal for articulated robots, packaging machinery, and space-constrained automation systems.
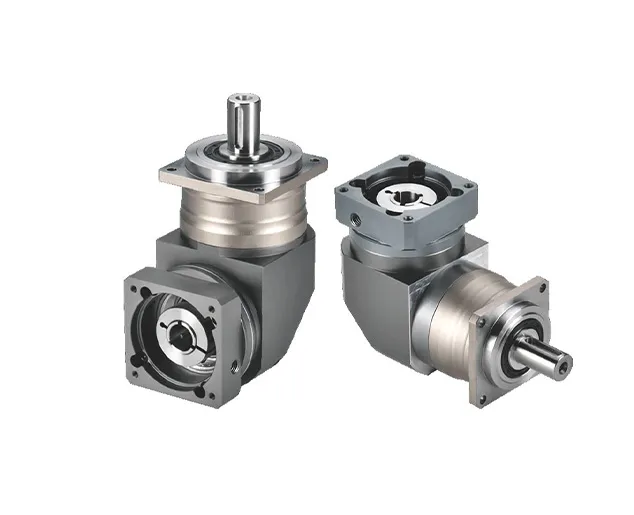
We Are Ready for Any Occasion
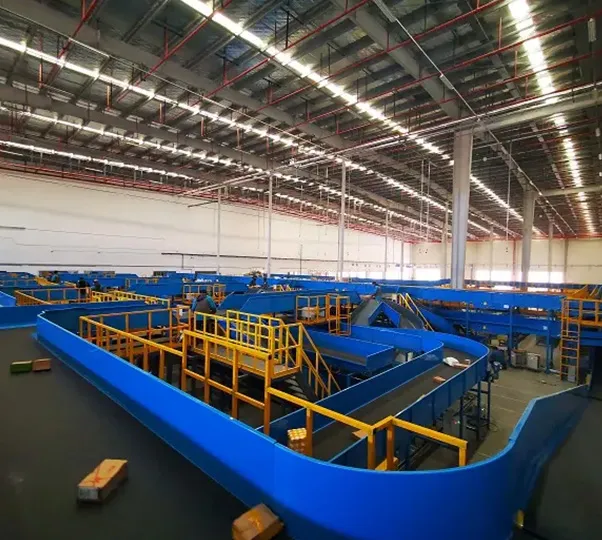
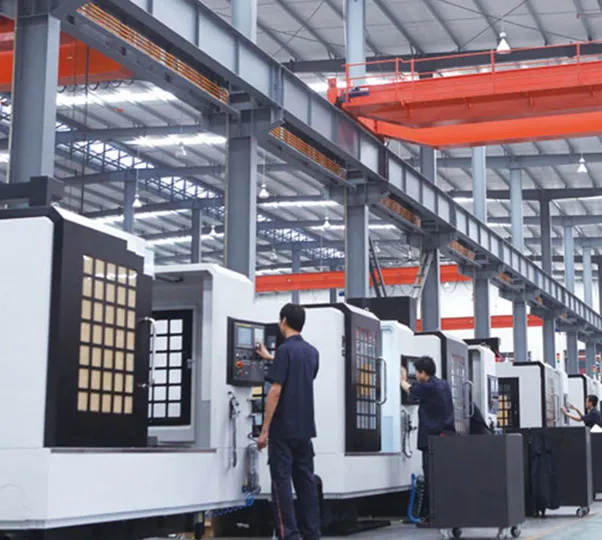
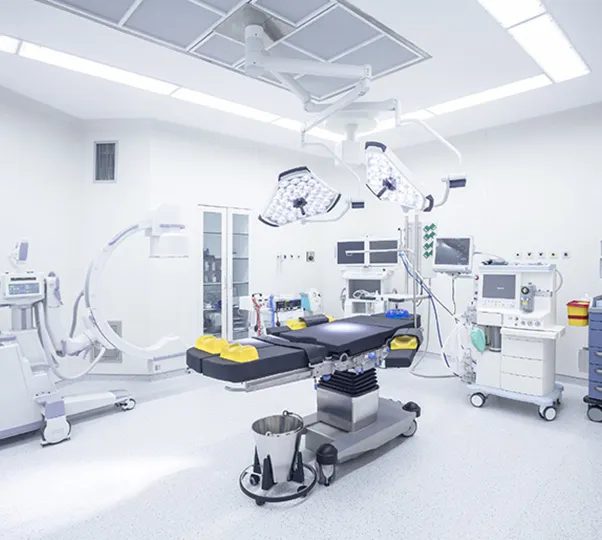
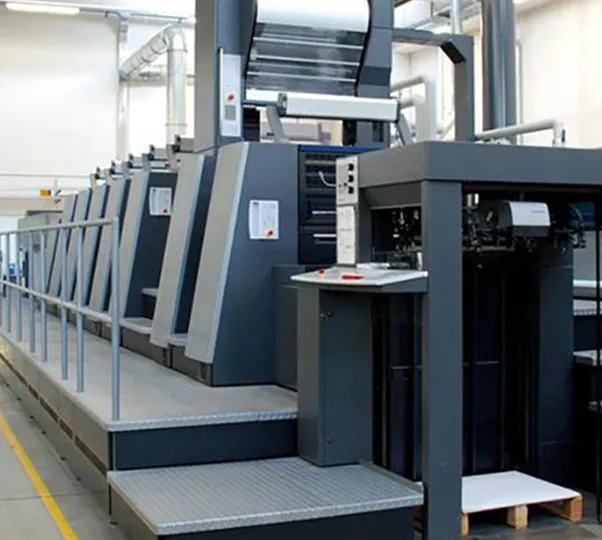
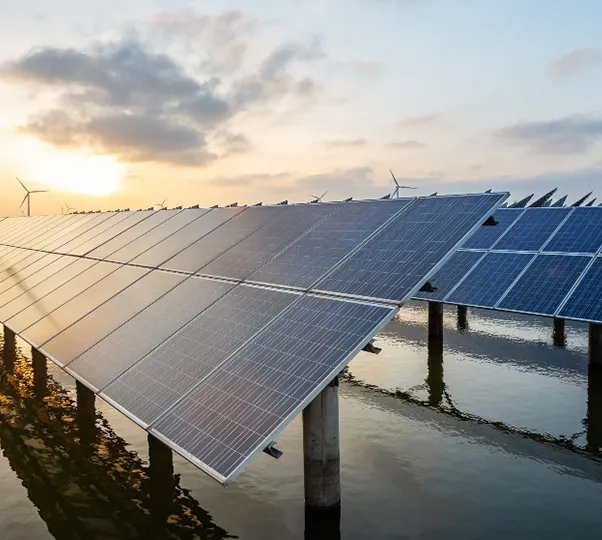
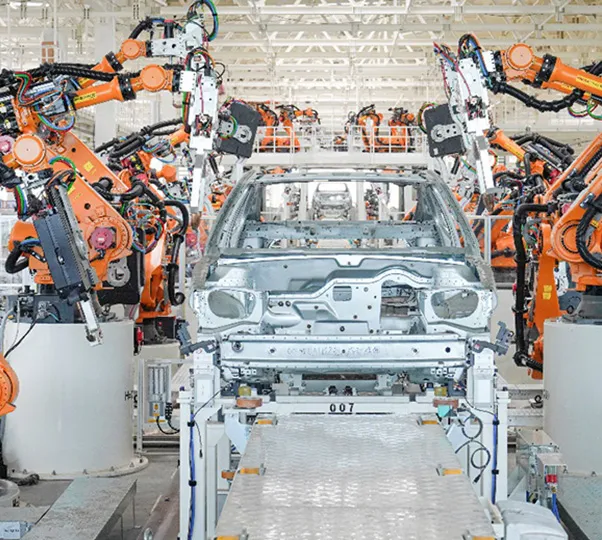
Features
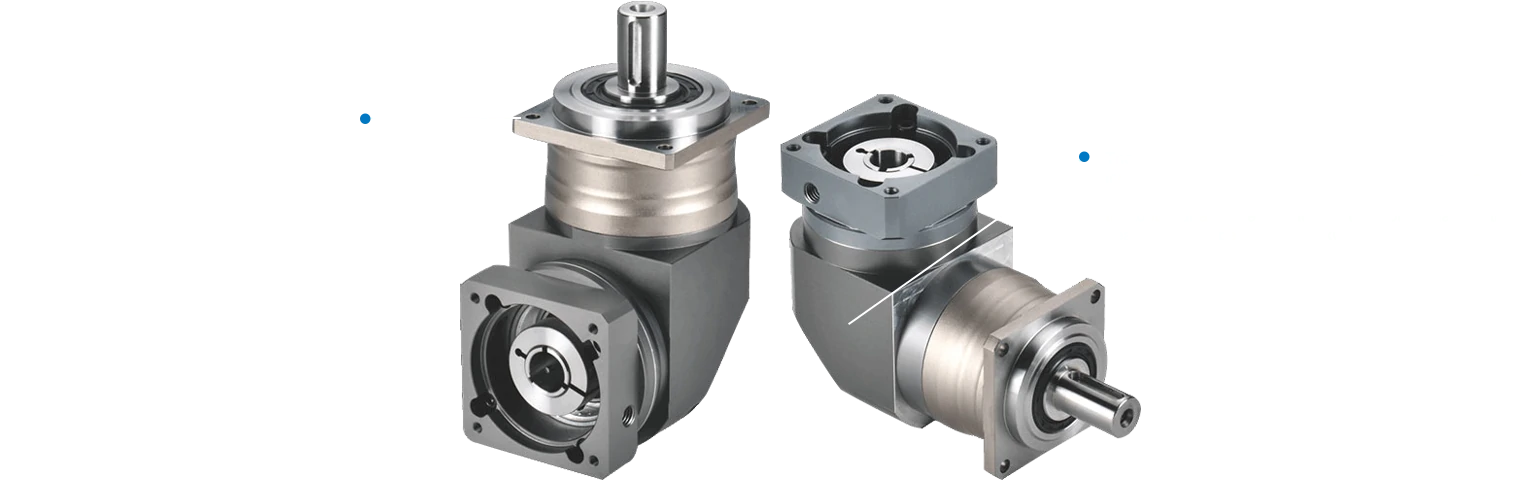
Right-Angled Helical Gear Reducer
01. VGZEK – Hollow Shaft Output, Round Flange
Features:
The reducer features an integrated structural design for the output flange and gear ring. Both the hollow output shaft and planet carrier adopt a dual-support cage structure with a wide-span bearing arrangement, delivering exceptional radial load capacity, excellent axial load support, and ensuring high rigidity and high positioning precision.
The right-angle housing incorporates double-row angular contact bearings on both ends, secured by locknuts to enhance the stability of the bevel gear assembly.
This series offers outstanding performance across all critical parameters, capable of withstanding high radial loads and moderate axial loads, making it ideal for high-strength, high-precision applications with frequent start-stop operations and varying load conditions.


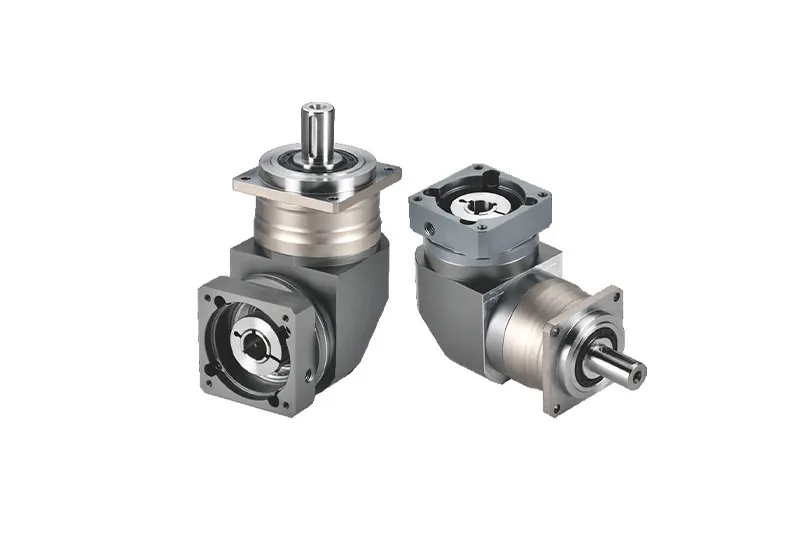
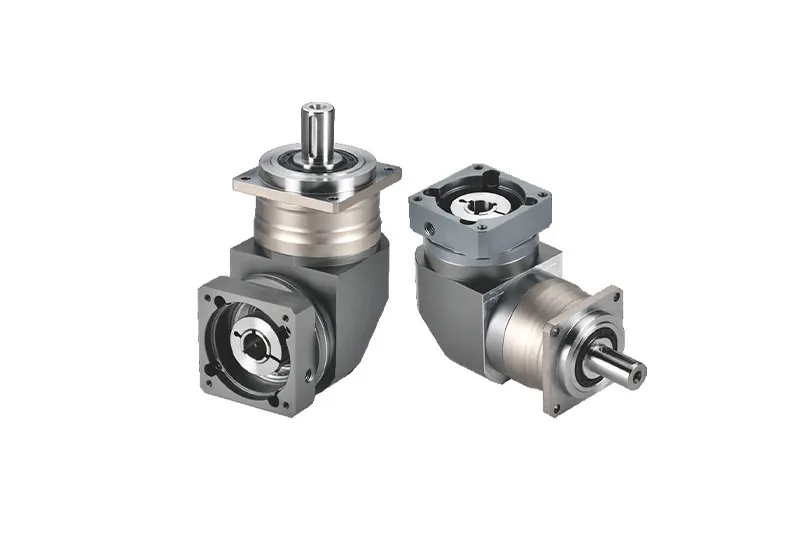
Customized Solutions for Right-Angled Helical Gear Reducer (L Shape)
Custom planetary reducers are designed to meet the unique demands of specialized industrial applications where standard gearboxes may not be sufficient. These demands may include specific working conditions, gear ratio requirements, space constraints, or additional functional needs. Our customization process follows the steps below:
- Requirement Analysis & Consultation
- Solution Design
- Technical Evaluation
- Prototype Manufacturing
- Performance Testing & Validation
- Design Optimization (if needed)
- Customer Approval
- Mass Production
- Delivery & After-Sales Support
Frequently Asked Questions
What are the reasons why a drive motor is not loaded?
What drying methods are there for gear motors?
In which steps is a gear motor installed?
How is the reduction gear heat treated?
What is the maximum transmission ratio of a planetary gearbox?