Shaft Grinding
Precision Shaft Grinding: Ensuring Accuracy, Durability, and Performance in VIGE Planetary Reducers
What Is Shaft Grinding?
Shaft grinding is a precision finishing process used to achieve exact dimensions and exceptional surface quality on cylindrical parts. This abrasive machining technique removes minimal material to ensure the shaft’s diameter, roundness, and straightness meet extremely tight tolerances. It is widely applied in high-performance gear manufacturing, where the quality of the shaft directly impacts system efficiency and reliability.
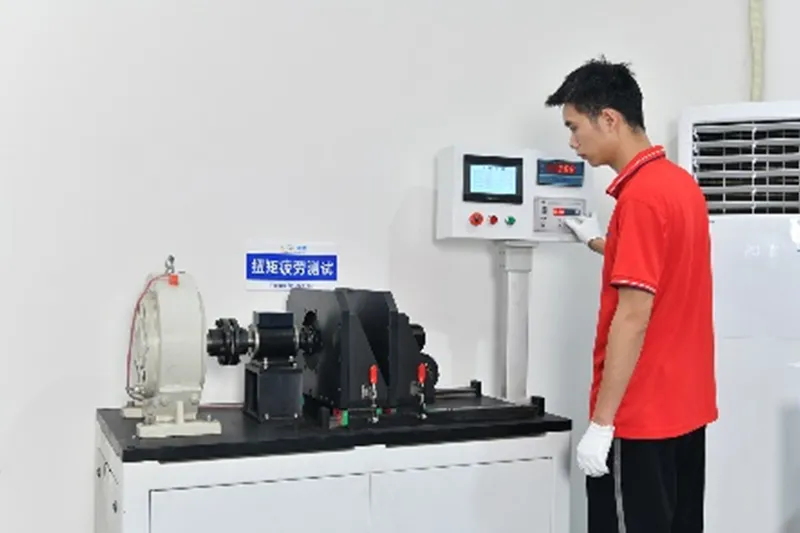
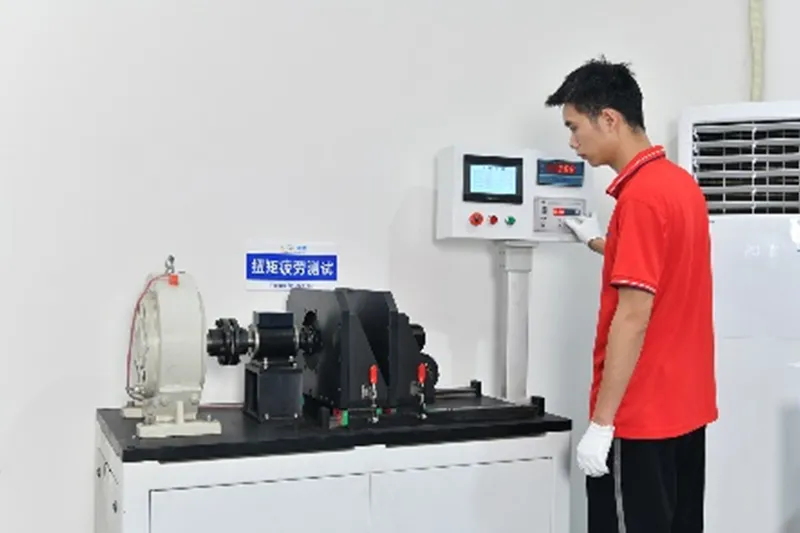
What Defines a High-Quality Grinding Process?
A top-tier grinding process is characterized by its ability to consistently produce shafts with:
- Tight dimensional tolerances (micron-level accuracy)
- Superior roundness and concentricity
- Ultra-smooth surface finishes (Ra ≤ 0.2 μm)
- No thermal distortion or surface burns
Key elements include proper wheel selection and dressing, optimized feed and speed control, and stable fixturing. Use of precision grinders, temperature-controlled environments, and real-time monitoring ensures repeatable, high-quality results.
Why Shaft Grinding Is Critical in Planetary Gear Reducers
In a planetary reducer, the shaft serves as a core transmission element. Its surface integrity and dimensional precision influence:
- Gear engagement accuracy and backlash control
- Bearing alignment and smooth assembly
- Fatigue resistance, reducing micro-crack risk under cyclic loading
- Corrosion protection, as smoother surfaces reduce moisture retention
- Noise and vibration reduction, improving overall operational stability
In high-speed servo systems or precision automation, these performance factors are essential for long-term reliability.
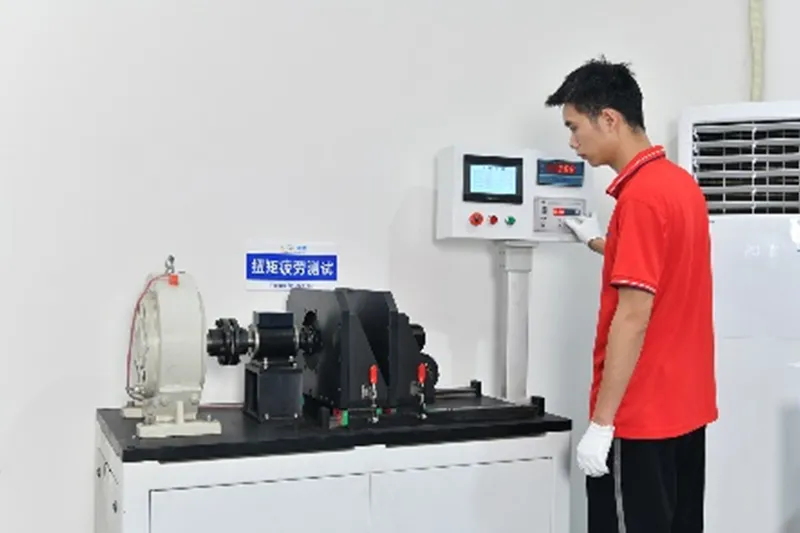
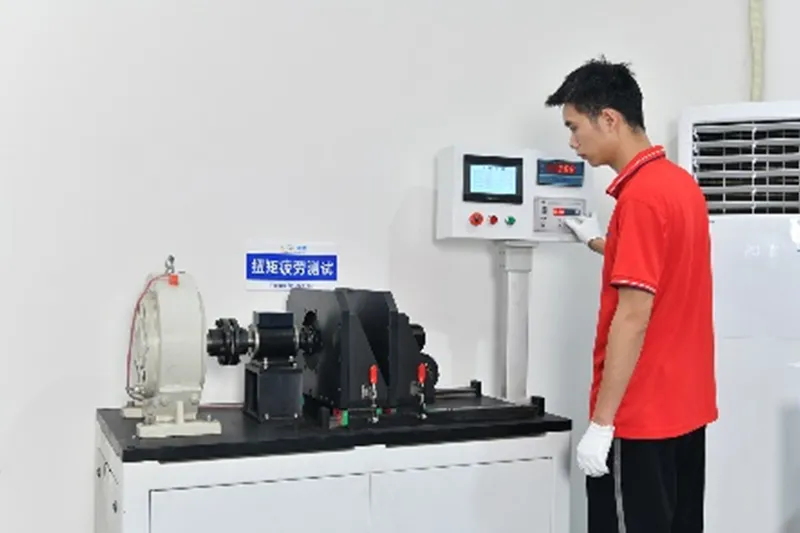
How VIGE Ensures Grinding Quality
At VIGE, we employ advanced shaft grinding machines with in-process measurement capabilities. Our process includes:
- CNC-controlled cylindrical grinders
- Real-time diameter and roundness feedback systems
- Surface finish testing (profilometers, optical inspection)
- Final dimensional verification using CMM and precision air gauges
All shafts are processed under strict environmental and quality control to eliminate geometric deviations and surface inconsistencies.
Additional Benefits of Precision Grinding in Production
By achieving optimal bore geometry and surface integrity, precision grinding eliminates the need for post-assembly rework or adjustment. It ensures seamless shaft fits and enhances overall gearbox symmetry, contributing to:
- Lower noise
- Longer bearing life
- Easier, faster, and more consistent assembly
This also reduces internal stress concentrations, helping improve fatigue resistance in dynamic gear applications.
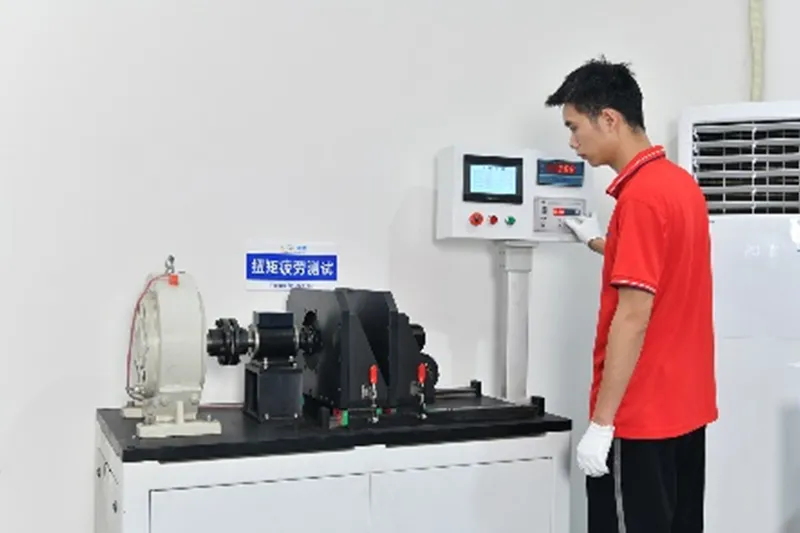